We use cookies to improve how you experience our website. Read more about our GDPR-policy here.
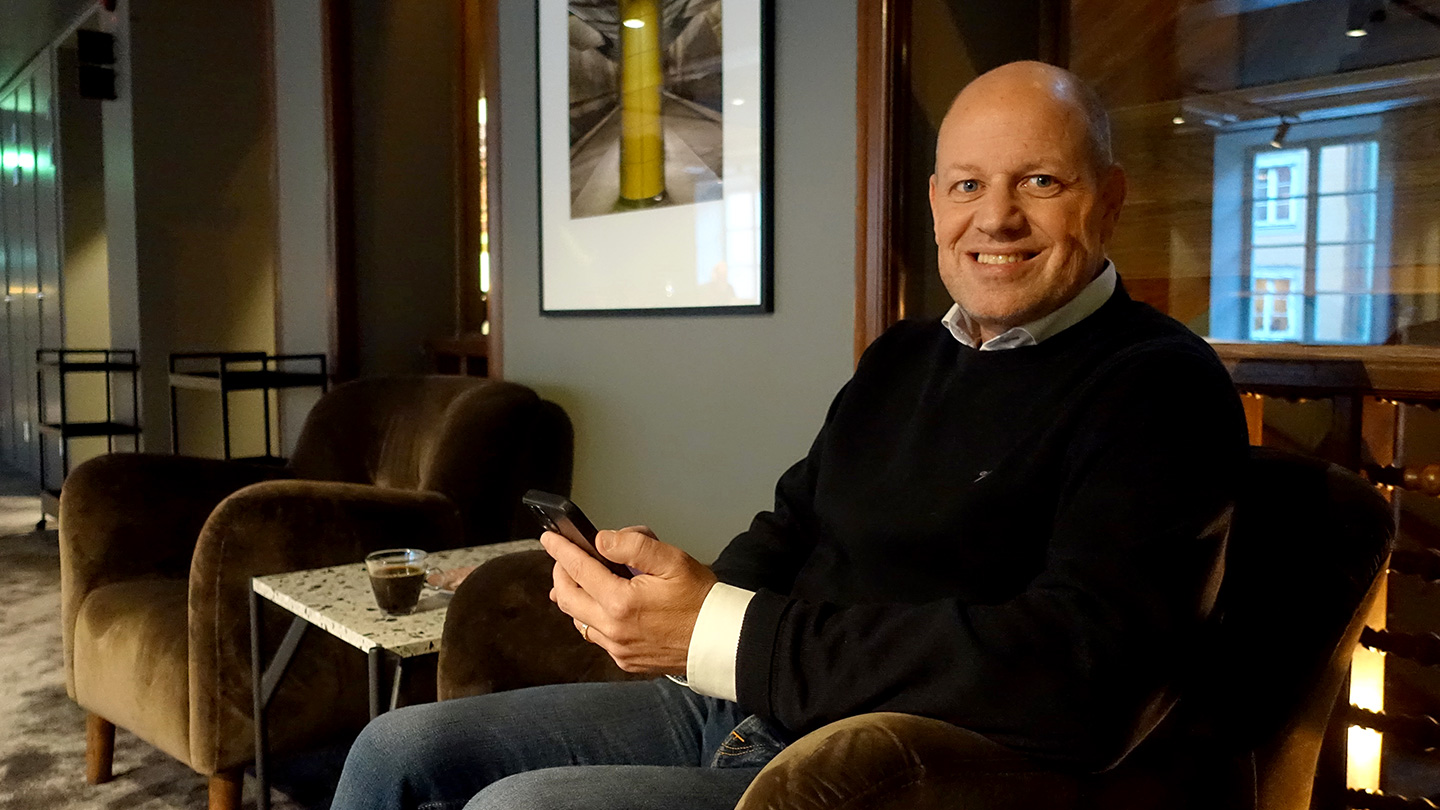
As Project Director, Daniel Finnson is focused on streamlining GreenIron’s processes with operational responsibility to ensure that things happen. This includes developing the company’s hardware; from design to commissioning of furnaces and heat exchangers.
“More specifically, it involves overseeing the construction of electrical rooms and transformers, as well as the design of hydrogen and nitrogen stations, monitoring systems, and much more, that will be installed at our factories,” says Daniel.
Daniel was born and raised in the nature-close and somewhat sleepy villa community of Storvreta, just north of Uppsala. In high school, Daniel attended a 4-year engineering programme, after which he went straight to the university in Uppsala for further studies in engineering. Three years later, Daniel could call himself an engineer with a bachelor’s degree in mechanical engineering.
“I was brought up in a family where everyone is in sales, and I have never been interested in technology nor had any particular career dreams. I was fascinated by technology in a broader perspective, since as an adult you could essentially become anything. Everything has just flowed on, perhaps thanks to my life philosophy being built on curiosity, seeing opportunities, and being able to make my own choices. Therefore, the focus on mechanical engineering has suited me to a tee,” says Daniel.
With the ambition to deepen his English language skills, Daniel moved to England in 1995 to take a Cambridge exam in English during the autumn term. During the day, there was full focus on the studies, but evenings and weekends were devoted to student parties, pinball playing at the pub, and league play in squash. With a diploma in English in his luggage, Daniel returned to Uppsala and took employment as a machine designer at Outokumpu Copper (former Svenska Metallverken) in the industrial city of Västerås, which, together with Asea, was founded at the turn of the last century and was involved in the electrification of Sweden at that time. Daniel devoted his workday to designing and drawing machines for foundries, rolling mills, and slitting lines.
“Here I got a broad technical education, much thanks to my mentor, a gentleman from Småland, with whom I shared an office,” says Daniel. “I remember listening keenly to his phone calls with big ears, accompanying him on trips, and attending meetings. An invaluable introduction for a rookie in the working life, which, unfortunately, hardly exists anymore.”
In 2001, an opportunity arose for Daniel to move to the Netherlands, a bit of a trainee year. There he worked as an operator in the foundry and spent a few months in the maintenance department, tinkering with and developing machines, among other things. Daniel soon grew into the role of project manager, a link between the design departments in the Netherlands and Sweden.
In 2003, Daniel moved back to Sweden and was appointed head of Outokumpu’s design department in Västerås after a couple of years. Daniel was asked if he would like to share his experiences for a week at Outokumpu’s launch in the USA. He did not hesitate for a second, packed his bag in no time, and stayed (part time) in the USA until 2008, with many more experiences under his belt. The last few months, Daniel was based in Columbus, Ohio, with the task of evaluating whether Outokumpu should continue its expansion in the USA or shut down operations. Finally, a decision was made to shut down, after painstaking calculation of production costs versus expected customer revenue.
“I remained loyal to Outokumpu (was acquired in 2011 by the German copper producer Aurubis) until 2013,” Daniel recounts. “During the last years, I worked as a project manager to integrate the production of radiator strip in Finspång with the operations in the Netherlands. Once production had started in the Netherlands and Outokumpu’s operations in Finspång were shut down, I realised that the metal industry had no future in Sweden. That’s when I received an enquiry about starting at the small Västerås-based company Radscan, which had an industrial focus on environmental technology and energy recovery from complex gases. It was a new and exciting area for me to explore. I stayed there for three and a half years, with a parallel goal of settling down in Västerås and drastically reducing the number of travel days.”
In 2017, Daniel moved to a position as a project manager at Ovako’s steel mill in Hofors. In November 2021, Daniel was contacted by GreenIron and initially Daniel was hired as a consultant. On April 1st 2022 Daniel commenced his position as a Project Director.
Daniel assumes that we will see a development over the coming years where, with the help of green technology, we strive to create sustainable industries, which in turn will lead to countless mergers, corporate acquisitions, shutdowns, and so on. However, Daniel is completely convinced that GreenIron has bet on the right horse, as the green transition and demand for smart technology entail an accelerating need for both base metals and critical minerals. Of course, we need to extract more and more metals from the earth’s crust, but it is an equation that does not add up in the long run if we are to achieve the goal of limiting the global temperature increase to well below 2 degrees before 2050. The flow of metals from mine to landfill needs to be replaced by a circuit, as the extractable metals are a finite natural resource. Daniel is convinced that the historically deeply rooted linear logic of the manufacturing and producing industries needs to be transformed to pave the way for a circular paradigm.
The greatness of the GreenIron process, thinks Daniel, is well summarised in the tagline ‘More Circularity. Less Mining’, as it clearly signals the company’s intended market position.
“As an engineer, I try to stand with both feet firmly on the ground. But if our industry were solely guided by technicians, probably not much would happen, as we are a questioning profession with high demands for optimised technical solutions and proven products. Sometimes I can certainly sound like a stuck record with my ‘hold on, we’re braking here’. But it feels extremely safe to know that the reduction process already works today, that we can reduce five tons of oxidised material in cycles of an hour. In a few years, I think we will have an extreme development curve, with furnaces each reducing carbon emissions by 56,000 tonnes per year. And in the longer term, I guess we will have up to 2,000 employees and run our own facilities worldwide. I truly believe in this, the sky is the limit,” Daniel concludes with a smile on his lips.