We use cookies to improve how you experience our website. Read more about our GDPR-policy here.
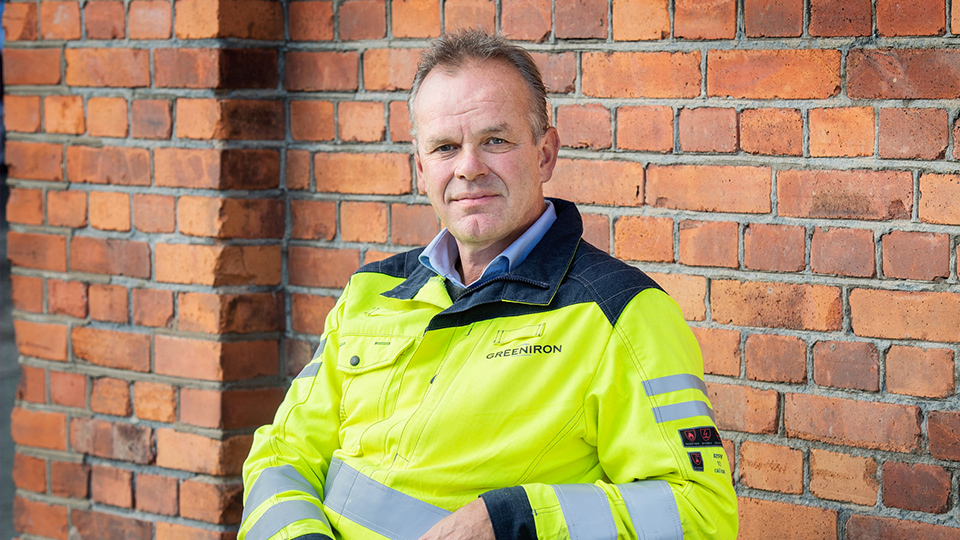
Jan Boberg is Creative Product Director at GreenIron, which fits him like a glove. The combination of a long and broad experience from the industry with an open mind, lack of prestige and curiosity, means that he is passionate about being involved in the company’s continued journey. Jan is today just as convinced of the greatness of GreenIron’s technology as he was three years ago, when he was first introduced to GreenIron.
Jan was born in Hallsberg and has belonged to a farming family in Närke for several generations. His interest in minerals and rocks was piqued as a young boy, in part when visiting ancient sites in the neighbourhood with his grandfather and collecting purple-colored amethysts by Lake Ärten, and in part by working in a zinc mine during summer holidays.
The passion for basketball and the love for nature and American 60’s music was awakened at a young age. In high school, the choice fell on natural sciences and thoughts revolved around becoming a geologist. But fate wanted it differently, instead he took a master’s degree in materials science at the Royal Institute of Technology in Stockholm with a specialisation in process metallurgy.
Although employment at Degerfors Järnverk had never appealed to him, Jan began working in the technical department with responsibility for continuous casting in 1987. Mergers and restructuring in the Swedish special steel industry led to a job at Avesta Sheffield AB, own foundry operations and another stay at the ironworks in Degerfors, now as head of metallurgy. Then marketing manager at newly formed Degerfors Stainless and recruited to Trelleborg Sigma. Changed career and opened a hugely popular restaurant outside Örebro. Back to the steel industry as technical manager at AST-Fagersta and site manager in Storfors. Later marketing manager at OSTP, CEO at ÖMV AB and vice president at Nordic Raw Material in Landskrona.
In early 2021, Edward Murray presented GreenIron’s technology to Jan. “I immediately saw the possibilities in recycling residual products – filter cloth and glow plugs – from the steel industry. A paradigm shift after 4,000 years of using hydrogen instead of carbon in the reduction of various metal oxides,” says Jan.
The test furnace had just been started up in Älvsjö, Sweden, and now began a period of successful attempts to convert various metal oxides into metals. During fruitful meetings, in the minimal office space on Regeringsgatan in central Stockholm, every imaginable stone was turned in order to improve the technology, additional patents were sought, new potential markets and products were defined. It was calculated on hydrogen and flows and brainstormed with the support of sketchpads and half-finished excel sheets.
Jan’s driving forces for being involved in the mining and steel industry’s green paradigm shift are primarily about contributing to making the steel industry internally circular and taking care of the waste streams generated during steel production. Filter dust and slag alone generate approximately 100 million tons of residual products per year, which could be returned as excellent raw materials to the world´s steel mills. The process is completely ground-breaking and the potential is therefore enormous, as the technology can also play a key role in traditional ore processing.
“My commitment to the environment and sustainability has been strong for several decades. I remember like yesterday a lecture at KTH, when one of the professors showed a diagram with the correlation between the carbon dioxide content in the atmosphere and the temperature increases during the 80s. You could clearly see that the carbon dioxide increase and the global temperature increase were followed,” says Jan. Something you weren’t convinced about at the time, but Jan was. Furthermore, scientists have known about the exact correlation between human impact and increased carbon dioxide levels for over 100 years. For Jan, the saying “No one can do everything, but everyone can do something” has served as a source of inspiration.
Jan’s vision is that in the future GreenIron’s furnaces will be found in all major steel mills in the 46 countries identified as potential markets. That GreenIron has written history by being pioneers in the early 2020s, taking the leading position in the mining and steel industry’s green paradigm shift and contributing to the industry becoming completely hydrogen-based. And that GreenIron has thereby contributed to significant reductions in the world’s carbon dioxide emissions.
Jan says that “the most important thing on the short term is that GreenIron builds a facility with large-scale production in 2024. And that the company’s stakeholders thus become aware that GreenIron has left the pilot stage and gone from idea to drawings to reality”.
This year, Hans Murray turns 90, who in the early 70s developed GreenIron’s innovative technology. It would be a well-timed 90th birthday present for this founder, known for his creative and innovative thinking. According to Jan, the fact that Hans invented this unique technology already in the early 70s is completely revolutionary. If the mining and metal industry had already understood the potential and all the stars were aligned, our industry today would have been 50 years ahead in technology development and would not have accounted for around eight percent of the world’s carbon dioxide emissions.
Jan concludes by saying “there is almost a Klondyke atmosphere at GreenIron. Everyone who is an employee of a pioneering company, with great potential and innovative technology, will be part of an extremely developing journey”.