GreenIron – literally squeezing water from stone
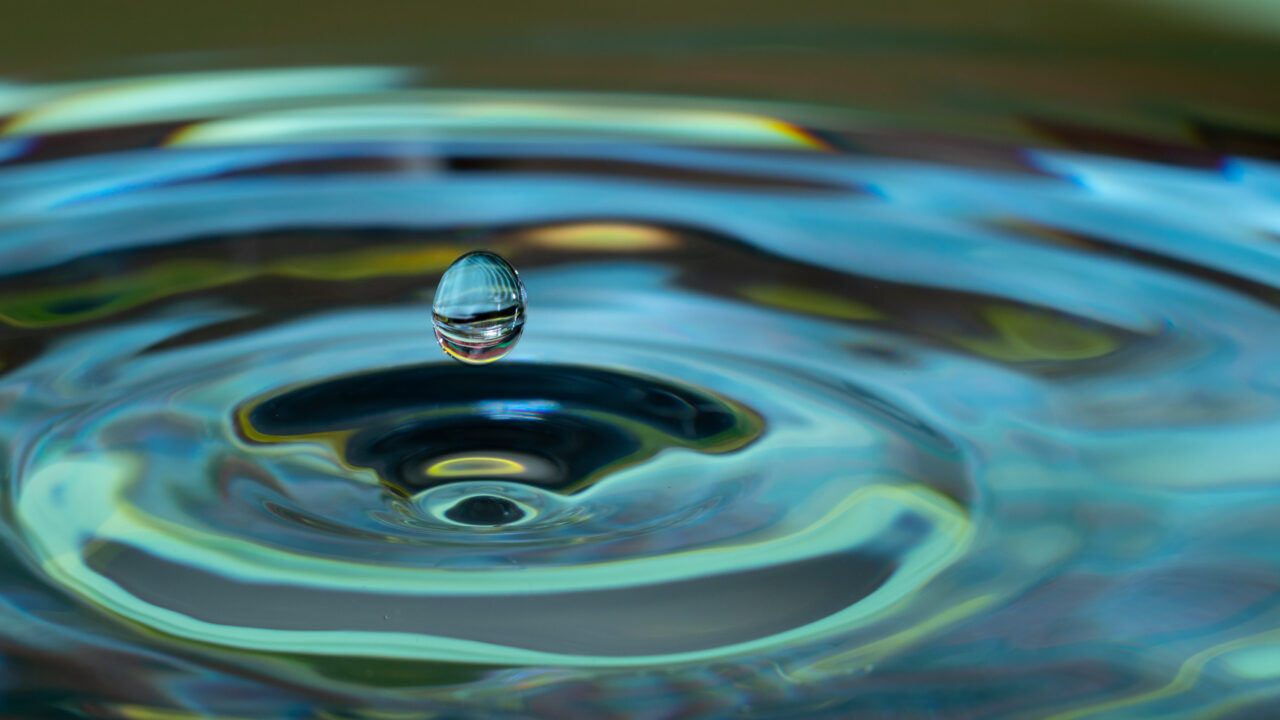
Today, on UN World Water Day, we take the opportunity to talk about GreenIron and our technology, where water stands as the sole residual product, literally squeezed from stone.
GreenIron aims to contribute to a greener mining and metal industry, and we do so using technology based on hydrogen. When we process, for example, iron ore in our furnace, we obtain a pure raw material in the form of iron (this applies also to other metals such as copper, nickel, and a few others) with water as our only residual.
The emissions in the metal industry originate from the process of removing oxygen from ore. We solve the problem of CO2 emissions by using hydrogen where carbon was previously used to reduce the oxygen. With our technology, we generate no CO2 emissions, thus potentially becoming a significant contributor to reducing the CO2 footprint of both the mining and metal industries.
“We become a complement to the mining and metal industries and create the possibility of producing fossil-free metal by converting ore from mines or residuals from manufacturing industries”, says Linda Ahl, CTO at GreenIron
For the mining industry, we can act as the fossil-free intermediary from, for example, iron ore to iron (so-called sponge iron), which then goes to the metal industry, where the iron is processed into steel in the steel mill. We can also extract metals from mining residues such as waste, mine tailings and landfills. For the metal industry, we can enhance resource efficiency and circularity by recycling metals from residues such as oxidised scale, grind shavings, filter dust and slag. After processing the residues in our GreenIron furnace, it can return into the steel production again.
How does it work?
Simply put, when hydrogen (H) in our furnace meets the oxygen (O) in the metal oxide (for example iron oxide, FeO) at the right temperature, hydrogen and oxygen reacts and forms water (H2O). The iron oxide in the input material is reduced, yielding the pure metal, and new water is formed – so, we literally “squeeze” water from stone. Although the water may be relatively clean when it comes out of our process, it cannot be classified as drinking water and may need some purification steps. Depending on the material we use, the water contains various substances that we purify, using water treatment technology.
“Right now, our focus is to get our production up and running, but in the future, we will certainly find useful applications for the new water we have squeezed out,” says Linda Ahl.
Facts
- For 1 ton of reduced iron, we create approximately 500 liters of water in our furnace and no carbon dioxide.
- According to the World Steel Association, the global steel industry produces about 2 billion tons of steel annually. About 5 % of the steel produced becomes oxidiced scale and filter dust. Today, most of these are discarded.
- Slag heaps = accumulations of by-products or residuals generated as a result of various industrial processes, especially in mining and metallurgy. Slag heaps usually consist of unwanted residuals that need to be removed from production facilities.
- Oxidised scale: small flakes of, for example, iron oxide that come off when steel is processed. Filter dust: iron-containing dust particles. Grind shavings: small, thin pieces of metal generated as waste during metal grinding or machining processes. Slag: various types of minerals and impurities originating from raw materials or formed during processes such as steel production.